Modular Homes: Cost-Effective & Customisable Alternative to Site-Built Homes
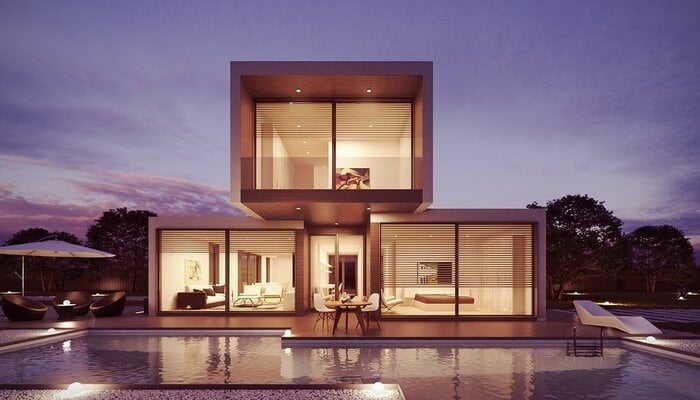
Table of Contents
Modular homes are a cost-effective and customizable alternative to traditional site-built homes. Constructed in factories, they adhere to the same building codes as traditional homes with the advantage of added quality control. They can be designed to be energy-efficient, resulting in long-term savings on utility bills. In this blog, we'll look at modular homes, how they differ from other prefabricated structures, how they're constructed, and the multiple benefits they offer.
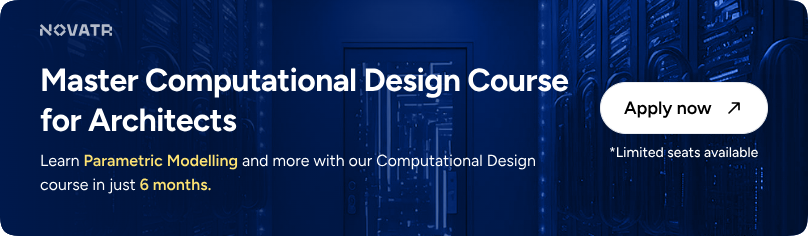
What are Modular Homes?
Modular homes refer to prefabricated or pre-built homes. These homes are constructed off-site in a factory setting, in modules or sections, and then transported to the building site for assembly.They are built following the same building codes and standards as traditional site-built homes, but the construction process differs. The modules are built in a controlled environment, ensuring consistency and quality control. The modules are assembled and finished on a solid foundation once they are delivered to the construction site. Modular homes can be customized to meet homeowners’ needs and come in various sizes and styles, from small, single-story homes to larger, multi-story homes. They are also built to be energy-efficient, resulting in potential utility cost savings. They provide a practical and affordable alternative to conventional site-built homes, with faster construction and potentially lower prices.
Read Also: What is Modular Architecture, Its Advantages, And 10 Examples (2025)
Modular Homes v/s Prefabricated Structures
Modular wooden houses and prefabricated structures are similar in that they are both built off-site in a factory or manufacturing facility. However, there is a difference between the two in terms of their construction and transportation.
Modular homes are built in modules or sections that are transported to the building site and assembled on a permanent foundation. These modules are typically built to meet state or local building codes, and the finished home looks like a traditional site-built home. On the other hand, prefabricated structure can refer to a variety of building types, including modular homes, but they also include other types of buildings that are prefabricated off-site, such as panelized homes, mobile homes, and even commercial buildings like office spaces or warehouses. These structures can be built using different materials, and construction methods, and they may offer varying levels of customization.
While modular homes are a particular type of prefabricated structure, they differ from other prefabricated structures in that they are constructed in modules that are transported and assembled on a permanent foundation. Additionally, modular homes are usually subject to more rigorous building codes and standards, because they are designed to be permanent residences and must comply with local building regulations. Modular homes are a type of prefabricated structure, but it is essential to note that not all prefabricated structures are modular homes.
Construction Process of Modular Homes
Modular homes are prefabricated homes that are built in a factory, in modules or sections, and then transported to the building site for assembly. Here's a detailed overview of the construction process:
Design and Planning: Design and planning are the first steps in the construction of a modular home. The modular home manufacturer and the owner collaborate to create a home that perfectly fits their requirements and tastes. The builder will prepare a thorough plan and drawings for the house using CAD software.
Factory Construction: The modular home is built in a factory setting once the design and planning phase is completed. The factory will have an assembly line where each module is constructed in a separate section of the factory. The modules are built using traditional building materials, such as wood framing, drywall, insulation, and roofing. Each module is built to meet state or local building codes and standards.
Quality Control: A stringent quality monitoring system is in place and inspects every step of the construction process to ensure that every module satisfies the most elevated standards of quality and workmanship.
Transportation: Once the modules are completed, they are transported to the building site on flatbed trucks. The modules are usually transported separately and may require permits and escorts. The modules are secured to the truck to prevent damage during transportation.
Assembly: Once the modules arrive at the construction site, they are put together on an already-prepared foundation. A crane is used to bring the modules into position, and they are subsequently attached to the ground and one another. To make the house weatherproof, the plumbing and electrical systems are linked, and the walls and roof have been sealed.
Finishing: This involves finishing the interior and exterior of the house, such as installing cabinets, floors, fixtures, etc.
Inspection: Modular homes are subject to the same building codes and regulations as site-built homes and must pass inspection by local authorities before they can be occupied. Once the modular home has passed inspection, it can be occupied by the homeowner.
Benefits of Modular Architecture
Modular architecture, also known as modularity or modular design, is a widely used technique in industries such as software development, engineering, and manufacturing. This approach involves breaking down a system or project into smaller, self-contained units called modules. Each module serves a specific purpose and can be developed independently, while still seamlessly integrating with other modules. The use of modular architecture offers numerous benefits.
1. Speed of Construction: Compared to traditional site-built homes or buildings, modular architecture is quicker. Since a large portion of the construction is carried out in a factory, there aren't any weather-related delays or other site-specific problems to worry about. As a result, modular homes and buildings can be finished in a matter of weeks as opposed to months.
2. Cost-Effective: Compared to traditionally constructed homes or buildings locally, modular architecture is less expensive. This is because the construction process is more simplified, requires fewer on-site workers, and the use of factory-produced modules results in less waste and mistakes during construction. Additionally, the materials used in modular architecture are frequently more environmentally friendly and long-lasting, which can reduce overall costs.
3. High Quality: Construction of modular homes and buildings takes place in a factory, enabling better quality control and precision. Building quality tends to be very high, and the modules are built according to national, state, and local building codes and standards. In addition, when compared with traditional houses or buildings, modular houses design, and structures are usually more energy-efficient, which may end up in savings over the long term and a lower environmental impact.
4. Flexibility: A high degree of flexibility in design and construction is possible with modular architecture. It is simple to alter the design or add additional components to the structure because the modules are prefabricated in a factory. Therefore, modular architecture is perfect for, including single-family homes and huge commercial structures.
5. Sustainable: Traditional construction methods are frequently less environmentally friendly than modular architecture. This is because modular construction frequently uses sustainable and eco-friendly materials, and the construction process produces less waste than traditional methods of building. In addition, energy-efficient modular building designs frequently end up in reduced long-term expenses as well as less carbon footprint.
Building Examples
In the modular architecture industry, companies like Mini Living, Tenfold Engineering, Blu Homes, and Method Homes are leading the way with their innovative approaches to design and features. They offer a range of unique options that cater to modular modern houses living preferences, while also promoting eco-friendliness and flexibility. These companies demonstrate the potential of modular construction to create stylish and efficient living spaces that are sustainable and meet the needs of today's lifestyles.
1. Mini Living
The modular architecture project known as Mini Living was created by the Mini car company. Urban areas will receive affordable and environmentally friendly living spaces thanks to the project. The Mini Living homes are made to be quickly put together and taken apart, giving residents flexibility in their living arrangements and mobility. The modules can be stacked and arranged in various ways to create living spaces, including studio apartments and multi-bedroom homes. Natural ventilation and environmentally friendly appliances are just a couple of the features that make the homes energy- and environmentally friendly.
2. Tenfold Engineering
David Martyn founded the modular architecture company "Ten Fold Engineering". The company produces modular buildings that are simple to transport and assemble on-site. Ten Fold Engineering's use of a patented technology that enables the designs to be folded up for simple transportation and storage is one of their distinctive features. These structures provide a variety of functions, including residences, workplaces, and educational facilities. They also have features like solar panels and natural ventilation to be environmentally friendly and energy-efficient.
3. Blu Homes
High-end, custom-designed homes are Blu Homes' area of expertise in the modular home industry. The houses are constructed in a factory before being transported and assembled on-site. The use of technology in the design process represents one of Blu Homes' unique features. Customers can view a 3D rendering of the finished product and customize their home design using an online tool. With elements like radiant floor heating and Energy Star-qualified appliances, the homes are also built to be energy-efficient.
4. Method Homes
Brian Abramson and Mark Rylant founded the modular home company, "Method Homes". Small cabins to enormous family homes are among the customizable home designs offered by the company. The attention Method Homes pay to sustainability is one of its distinguishing qualities. Solar panels, recycled materials, and low-VOC paints are just a few of the eco-friendly and energy-efficient features included in the home's construction. To further personalize homes, These Homes also provide a variety of finish choices, ranging from metal panels to natural wood siding. The business offers a variety of accessory dwelling units (ADUs) that can be rented out, used as guest houses, or as home offices.
In Conclusion
Modular homes provide an innovative and efficient solution for modern housing needs. With their off-site construction process, these homes offer a faster and cost-effective alternative to traditional site-built homes. The controlled factory environment ensures consistent quality, and the customization options allow homeowners to design their dream homes. The benefits of modular architecture extend beyond residential applications, as seen in noteworthy examples like Mini Living, Ten Fold Engineering, Blu, and Method Homes. These companies showcase the versatility, sustainability, and flexibility modular architecture offers. As the demand for efficient and eco-friendly housing solutions continues to grow, modular homes are likely to play an increasingly significant role in meeting these needs. With their streamlined construction process, high quality, and sustainability features, modular homes are revolutionizing the way we think about modular housing and construction.
Computational design has improved the efficiency and quality of modular home construction. By streamlining the design and assembly process, builders reduce costs and speed up production times while still delivering high-quality homes. Novatr provides a Masters in Computational Design course that helps in the development of complex geometric forms and optimizing design workflow using automation, parametric modeling, and generative design.
Frequently Asked Questions:
1. What is the concept of modular housing?
Modular house refers to prefabricated homes that are created in sections called modules offsite and then transported to the location for assembly. They follow the same building and construction code but require less labor resulting in a lower carbon footprint.
2. What are the three types of modular architecture?
The three types of modular architecture are:
- 2D Panels - It is the most common type of modular architecture as it is cost-efficient and easy to transport.
- 3D Modules - They are unique in the sense that they are 85-90% complete and furbished when they leave the factory. Thus not much work is to be done on them on-site.
- Hybrid Modular Construction - This is a mix of 2D panels and 3D modules. Combining their efficiency and productivity respectively.
3. What is the advantage of modular construction?
There are multiple benefits of modular construction including quality and speed. Because the module sections are created off-site in a controlled setting, the quality is better as well as the speed at which these modules are made is faster. Moreover, sustainability is an important aspect that is kept in mind while creating modular homes.